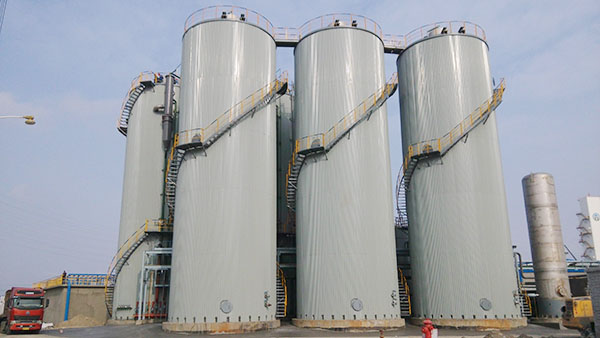
Upflow anaerobic sludge bed reactor is a kind of anaerobic biological method for sewage treatment, also called upflow anaerobic sludge bed, which is abbreviated as UASB (up flow anaerobic sludge bed / blanket). Invented by Professor lettinga of the Netherlands in 1977.
Sewage flows through UASB from bottom to top. There is a sludge bed with high concentration and activity at the bottom of the reactor. Most of the organic pollutants in the sewage are degraded into methane and carbon dioxide through anaerobic fermentation. Due to the agitation of water flow and bubbles, there is a sludge suspension layer above the sludge bed. A three-phase separator is arranged at the upper part of the reactor to separate digestion gas, digestion liquid and sludge particles. The digestion gas is led out from the top of the reactor; the sludge particles slide and settle automatically to the sludge bed at the bottom of the reactor; the digestion liquid is discharged from the clarification area. UASB has a large load capacity and is suitable for the treatment of high concentration organic wastewater. The UASB with good operation has a high removal rate of organic pollutants, does not need stirring, and can adapt to a large range of load impact, temperature and pH changes.
UASB anaerobic reactor structure
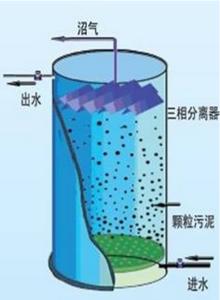
The important equipment in UASB reactor is three-phase separator, which is installed on the top of the reactor and divides the reactor into the lower reaction area and the upper sedimentation area. In order to achieve satisfactory settling effect of sludge flocs / particles in the upflow in the precipitator, the first main purpose of the three-phase separator is to effectively separate the biogas generated from the sludge bed / layer as much as possible, especially in the case of high load, the role of the reflection plate under the gas collecting chamber is to prevent the biogas from escaping to the settling chamber through the gap between the gas collecting chambers, in addition, the baffle also It is beneficial to reduce the liquid flocculation caused by the high gas production in the reaction chamber. The design of the reactor should be that as long as the sludge layer does not expand to the precipitator, the sludge particles or flocculent sludge can slide back to the reactor (it should be recognized that sometimes the sludge layer expands to the precipitator is not a bad thing). On the contrary, the expanded sludge layer in the precipitator catches the dispersed sludge particles / flocs, and at the same time, it also plays a certain role in the removal of biodegradable dissolved COD). On the one hand, it is very important to have a free space for the expansion of sludge layer to prevent the loss of heavy sludge under the impact of temporary organic or hydraulic loads. Both hydraulic and organic loading rates affect the expansion of sludge layer and sludge bed. The principle of UASB system is based on the formation of sludge flocs with good settling performance, combined with the setting of sludge settling system in the reactor to separate the gas, liquid and solid phases. The formation and maintenance of sludge with good sedimentation performance (it can be flocculent sludge or granular sludge) is the fundamental point for the good operation of UASB system.
Accessory equipment
1. The residual biogas burners are generally not allowed to discharge the residual biogas into the air to prevent air pollution. If there is any residual biogas that can not be used, a residual gas burner can be installed to burn it. The burner shall be installed in a safe area, and valves and flame arresters shall be installed in front of it. Residual gas burner is a kind of safety device, which can automatically ignite and extinguish fire. Generally, the distance between the residual gas burner and the digester cover or gas storage tank shall be at least 15m, and it shall be set in the open ground easy to monitor.
2. Anaerobic digestion of heat preservation and heating equipment, like other biological treatment processes, is greatly affected by temperature, and anaerobic process is more significantly affected by temperature. The optimal temperature range of medium temperature anaerobic digestion is from 30 ℃ to 35 ℃. It can be calculated that the digestion rate at 20 ℃ and 10 ℃ is about 35% and 12% of the maximum value at 30 ℃ respectively. Therefore, the importance of heating and heat preservation is self-evident. It is necessary to install a heat exchanger if there is available waste heat in or near the plant or if it is necessary to collect the efficiency from the middle of the effluent.
3. In order to improve the operation reliability of the anaerobic reactor, the monitoring equipment must be equipped with various types of measuring equipment and instruments, such as the control of water inflow, dosing and other measuring equipment, pH meter (pH meter), temperature measurement and other automatic instruments. Automatic metering equipment and instruments are the basis of automatic control. There are two main purposes of monitoring UASB reactor: one is to understand the situation of water in and out, so as to observe whether the water inflow meets the process design; the other is to control the operation of each process and judge whether the process operation is normal. Due to the particularity of UASB reactor, some testing items should be added, such as volatile organic acid (VFA), alkalinity and methane. However, these devices belong to the standard equipment, some of which are difficult to form online measurement and control.
Working principle
UASB reactor waste water is introduced to the bottom of the reactor as evenly as possible, and the waste water flows upward through the sludge bed containing granular sludge or flocculent sludge. Anaerobic reaction takes place in the process of contact between wastewater and sludge particles. Biogas (mainly methane and carbon dioxide) produced in anaerobic state causes internal circulation, which is beneficial to the formation and maintenance of granular sludge. Some gases formed in the sludge layer adhere to the sludge particles, and the attached and non attached gases rise to the top of the reactor. The sludge rising to the surface impacts the bottom of the gas transmitter of the three-phase reactor, causing the sludge floc with bubbles to degas. After the bubble is released, the sludge particles will settle on the surface of the sludge bed, and the attached and non attached gas will be collected to the gas collection chamber of the three-phase separator at the top of the reactor. The baffle placed under the gap of the gas collecting chamber unit acts as a gas emitter and prevents the biogas bubble from entering the sedimentation area, otherwise, it will cause flocculation in the sedimentation area and hinder the particle sedimentation. The liquid containing some residual solids and sludge particles enters the sedimentation area through the gap of separator.
As the flow area of the inclined sedimentation area of the separator increases near the water surface, the rising velocity decreases near the discharge point. Due to the decrease of flow rate, sludge flocs can be flocculated and precipitated in the sedimentation area. To some extent, the sludge flocs accumulated on the three-phase separator will exceed the friction force on the inclined wall, which will slide back to the reaction area, and this part of sludge will react with the influent organics.
On the basis of engineering practice, through digestion and absorption of advanced technology, our company reformed and innovated the structure of traditional UASB reactor, and reached a high level in the treatment of high concentration organic wastewater, which has been successively applied to large starch plants and biopharmaceutical plants (avermectin, vitamin